A lot of energy is needed to grow plants indoors. It’s important to use the appropriate heating or cooling system when designing an indoor cultivation facility. Systems come in a variety of varieties, including direct expansion (DX), split systems, VRF, hydronic, and more. This article will explain what grow room HVAC systems is and its benefits.
HVAC cultivation systems must be made to manage not only temperature and humidity, but also odors and airflow by using bi-polar ionization, ozone generators, or UV light. Learn more by continuing to read.
Table of Contents
How Does Hydronic Cooling Work?
Hydronic systems’ air handling parts function similarly to conventional air conditioners. Air from a hot, humid room is passed over a heat exchanger to remove heat and humidity. The room is then refilled with the cool, dry air. However, in hydronic systems, water is used as the heat exchange medium in the air handlers or fan coils instead of refrigerant. The heat exchanger in a chilled water system transfers heat from the air to the water.
The heated water then exits the room via a system of sealed pipes. It is delivered to a chiller plant, dry cooler, or other central unit where the heat absorbed by the water is rejected to the outside and cold water is returned to the air handlers or fan coils inside the building. Chiller plants are typically found outside of the building, though some water-cooled or heat recovery units may be found there, usually in a special mechanical room.
You May Also Like: Grow Room Cost Calculator
HVAC Systems and Energy Consumption
To keep growers’ design setpoints, grow room HVAC systems must regulate and match the sensible and latent process loads. The growers select the room design setpoints based on plant genetics and crop yields because they are aware that grow environments have an impact on crop characteristics.
The First Law of Thermodynamics, a physics-based version of the Law of Conservation of Energy, will be useful to readers to remember. According to the Law, a closed system’s total energy is constant; energy can only be changed from one form of existence to another and cannot be created or destroyed. No matter what kind of crop is being grown, this Law serves as a guiding principle for HVAC engineers and equipment manufacturers when designing systems to control temperature and humidity in grow rooms.
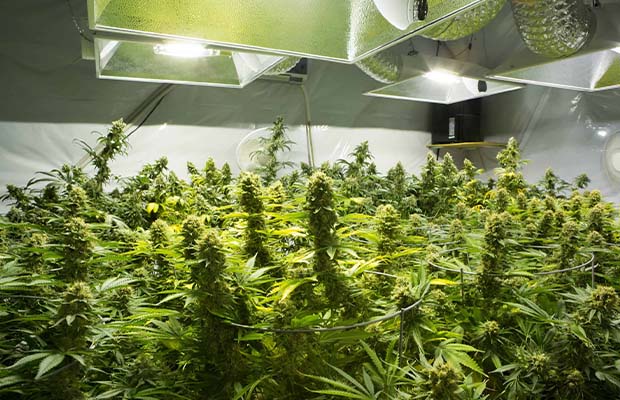
The comparison of four different HVAC systems’ energy usage that follows looks at all of the major operating modes. The impact of plants’ transpiration process on the temperature of the room is also examined in this discussion of energy consumption. The comparison is based on a grow room that is installed inside of a larger building and has insulated walls and a ceiling.
Energy considerations included in the comparison include:
- Electrical energy input to the air conditioners and/or dehumidifiers
- Heat always added by portable dehumidifiers (System A)
- Cooling of the enhanced dehumidifier with heat exchanger (System B)
- Cooling of the grow room zone via plant transpiration
- Heat required to overcome lights-off transpiration (Systems A, B, C)
Read More: The Effects Of Too Much CO2 In A Grow Room
Can a Hydronic System Be Used for Heating?
Indoor farms in cooler climates will still need to add heat to their gardens during the cold months if they want to be able to harvest all year round, even though grow lights and plant transpiration can produce their own heat.
Yes, heating systems using hydronics are possible. These systems employ water to move heat from one location to another, just like cooling does. In hydronic heating, the water is either heated within the central unit and then sent to the fan coils or air handlers in the grow room, or it can be heated within the units of the room. When the air in the room passes over the heat exchanger, the heat from the water is taken out and transferred to the air.
This procedure calls for units with both cooling and heating capabilities, and there are several ways to do this. Electric heaters that produce heat through electricity can be installed in fan coils and air handler units, but they do not use hydronic heat to do so. For that, they need a different set of pipes that enable heated water from the central unit outside the space to enter the grow space using the same procedure as the chilled water.
When we describe 2-pipe and 4-pipe chilled water systems as being different, that is what we mean. A two-pipe chilled water system uses units with two pipes: one for the cooled water to enter and one for the water to exit after removing the heat from the air. Two additional pipes—one for the heated water to enter and one for the water to exit after the air has lost its heat—allow a four-pipe chilled water system to perform hydronic cooling and heating.
Why Choose a Hydronic System?
Hydronic systems can be a practical and efficient choice for cooling, heating, and dehumidifying your indoor farm. In order to increase energy efficiency in cultivation operations, they provide a variety of free cooling options (without the need for ventilation in the cultivation space), integrated dehumidification, and high efficiency, industrial grade chiller plants.
Furthermore, you have the option to combine your irrigation system and chilled water HVAC system. Durango Cannabis Company actually followed through with this. The water that their dehumidifiers have collected can be recovered and used to re-water their plants. They can achieve a $30 average monthly water bill by reducing their water waste.
Additionally, hydronic systems offer a lot of flexibility in terms of how you can handle the air and how you can change things up as conditions change. Ductless options can be integrated, even in very large systems, unlike refrigerant-based systems where compressor and fan coil tonnage must be closely correlated. In hydronic systems, there are countless combinations of air handler sizes that can be used within a specific tonnage of compressors.
The fact that chilled water cooling and heating utilizes water pipes rather than voluminous ductwork is an additional benefit. Chilled water’s ability to efficiently and quickly move BTUs is one of the key distinctions between hydronic and forced air systems.
An ASHARE study found that a 3-in. diameter chilled water pipe can carry 1,000,000 Cooling BTUs while a 70-in. x 46-in. air duct would be necessary to accomplish the same task with air. Water is a better thermal conductor than air, which explains why.
To move water around the building in the ASHARE example, a 2 horsepower pump may be necessary. In a forced air system, 60-100HP fans would be required to move the air as needed. This illustration shows how chilled water requires significantly less horsepower (transport energy) than hot water to move BTUs. This promotes energy conservation and flexibility in obtaining capacity where and when it is required.
How Much Does It Cost?
The hydronic train may be calling your name if you’ve read this far. However, it’s crucial to consider all of your options before making a decision.
For many growers, hydronic systems can be a fantastic choice. However, there are a lot of factors to take into account when setting a budget for your mechanical system. A water cooled system can have a high initial investment, despite being one of the more effective and adaptable methods for temperature control. Choosing a company to install everything will also require extra caution because the application of hydronic systems calls for specialized knowledge. It’s challenging to put a price on something with so many different factors. The cost of a hydronic cooling system can vary depending on a number of factors, including the size and location of your facility, the required infrastructure, the timing of lighting and watering, the equipment you choose, and more. Always keep in mind that you have a variety of HVAC system options, so consult with a team of mechanical engineers to determine which one is best for you.
FAQs
Can You Have Too Much Airflow in a Grow Room?
While too much air movement can cause steam breakage, leaf tearing and growth in different directions, It is advised by Quest that you maintain a constant air flow in your grow up to that threshold.
Do Grow Rooms Need to Be Air Tight?
A sealed room is a growing environment without any openings or air exchanges to the outside or any other room, and its basic concept is quite straightforward. It doesn’t need to be airtight, however, the closer to airtight the better.
Final Words: An Efficient Option
Finally, there are numerous options for heating and cooling your indoor farm. Using less energy and water is possible with a hydronic system. They can also do away with the need for ductwork, saving room and lowering contamination risks. This also has the added advantage of controlling odor for cannabis growers. Nevertheless, these systems might be expensive.
Therefore, when deciding whether hydronic cooling is the best option, it’s crucial to collaborate with a skilled MEP engineer. Before deciding on the kind of system that will work the best for your farm, you should consider your geographic location, the availability of infrastructure, the necessary climate parameters, your access to water, odor regulations, local codes, and more. To learn more about grow room, read our below posts: